Loose Wires
Unstitching time. We have decided twisting copper wires between two sheets of plywood does not a watertight boundary make, and so are going to replace them with some nice watertight epoxy.
There are different approaches to getting the epoxy holding the hull together in place of the wires, which ideally you don’t leave in the hull where flexing and temperature changes can cause them to work their way through any nice fiberglass you put on top of them. Sounds good, but how do you meanwhile hold the hull in shape to do the switcheroo?
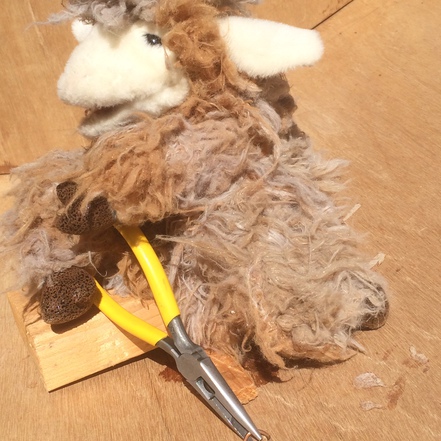
One option is to just epoxy over the wires and pull them out either while or after it cures. I have gotten all manners of things stuck in epoxy, which can be pretty determined stuff. When that happens with the wires, the standard approach is to take a torch to the wire which deflects the epoxy’s grip and loosens the wire. While a very common technique and nothing to fear, I am just not super keen on my skills at waving a torch around my boat. Furthermore, I used a good amount of thick 12 gauge copper wire since I got a deal on some I could repurpose (some of which probably literally fell off the back of a truck.) Meaning: they’re hard enough to yank out of the wood even without the epoxy.
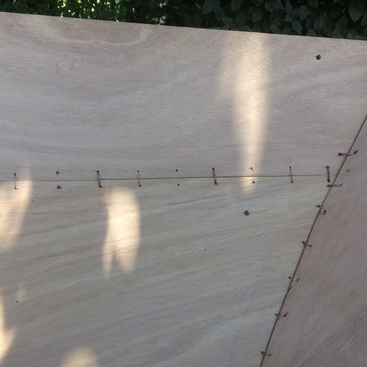
Because of that, I’m going with the other option which is to tab, like a welder would, the form into place with small tabs of epoxy along key points of the seam. Then remove the wires and then we’ll tape it into place.
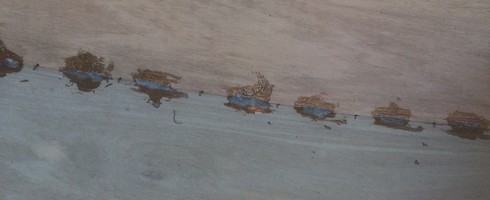
just as soon as we get that glass tape measured and cut..
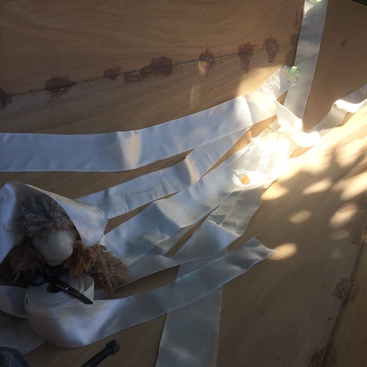
it might be a while..